how to choose plasma cutting and flame oxy-fuels?
What is flame cutting machine?
Flame cutting machine mainly use on heavy industries base,Flame cutter use oxygen,propane and methane gas.
Considering of economic cost most of users like more propane. Whatever hand flame cutter or mechanical flame cutting machine cutting torch is mainly tools.
Jinan allwin cnc machinery company provides all types of CNC mechanical flame cutting machine.
What is plasma cutting machine?
Plasma cutter is widely use in automobiles,locomotives,pressure vessels,chemical machinery,nuclear industry.
general machinery,construction machinery,steel structure processing,ships and other industries.
Plasma arc cutting is a processing method that uses the heat of high temperature plasma arc to locally melt (and evaporate) the metal in the workpiece incision,
and eliminates the molten metal by the momentum of high speed plasma to form the incision.so giving a proper plasma generator is the most important issue.
Jinan allwin cnc machinery mainly produce CNC plasma cutting machine..
CNC metal plasma cutter could cut automatically according to given procedure.
Cnc cutting machine consist of cnc system and mechanical framework.
1. The advantages of the flame cutting machine:
The cutting surface has good verticality, can cut thicker carbon steel, and the price is kinda of cheap;
Compared with plasma cutting and laser cutting, flame cutter could cut thicker metal sheet like carbon steel iron steel,aluminum,brass but their cost is the cheapest; flame cuts will use oxygen and propane (or acetylene) when work;
being user better choose flame or oxygen cutter if your steel materials is above 50mm thickness because of product cost is economics.
2. How to choose between plasma cutting and flame(oxy-fuel gas)
1) Plasma cutting is mainly used to cut thin metal plates with a thickness of less than 50mm, such as carbon steel, stainless steel, aluminum and its alloys and other metal materials;
generally, its better to choose plasma cutting machine if your metal plates is less than 50mm thickness because of high efficiency its cutting speed is upto 10m/min
its cutting speed is much faster than flame cutter ;
secondly its cut surface is more clean and its notch is narrow than other cutting methods&its deformation is very small.
Plasma cuts is supporting to cut in the water. Its deformation will be Zero if we put plasma cuts in the water we here called water plasma cutter or water plasma cutting it could help us to decrease deformation also remove smoke..alone with plasma source technology developing more and more very high precision plasma torch or gun come up..So far according to our experience in metal cutting industries plus many years manufacturing knowledge or feedback from our thousands customers end users or distributors from all over the world.we here advice some brands for plasma generators(plasma source).
1. Chinese brand plasma generator for (Quality cutting thickness for carbon steel)
Note:Quality cutting thickness is not same as maximum cutting thickness.
- 63A cutting thickness: 0-10mm
- 100A cutting thickness: 0-12mm
- 120A cutting thickness:0-15mm
- 160A cutting thickness: 0-20mm
- 200A cutting thickness: 0-30mm
- 300A cutting thickness: 0-40mm
- 400A cutting thickness:0-55mm
Maximum cutting thickness is 2 times of its quality cutting thickness for example 120A plasma power could cut 25mm maximum at very slow speed..over burden cutting thickness will cut its life.
We strongly advice users don’t let your cutting machine work overload.
If you are new user for plasma cutting machine or you don’t know how to choose plasma generator you can use these parameter for your reference ..Quality cutting thickness is the most important performance indicator not maximum capacity to cut.
USA Hypertherm power
- 65A cutting thickness: 0-12mm
- 85A cutting thickness: 0-16mm
- 105A cutting thickness: 0-18mm
- 125A cutting thickness: 0-20mm
- 200A cutting thickness: 0-30mm
their works stable with clean cuts and very reasonable price.
after we talked too much about plasma cutting and flame .we believe you should know how to choose here let us conclude again:
As we described earlier that if your steel material is over than 50mm cosidering production prices please choose flame oxygen-fule cuting
because 500A or 700A plasma source is very high meanwhile
bigger plasma generator 300A or 400A require workshop has strong electricity system with bigger size cable diameter.otherwise,It will effect your cutting smooth.
Generally speaking,their consumbles like tips nozzles and electrodes and caps any wearing parts is a little higher price than smaller ones from smaller plasma power.that is why most of users like more flame cutter for 50mm thickness material.
2)The flame cutting machine is mainly used for cutting thick plates, however, Flame cutter can not cutting stainless steel…So most of metal steel industries use plasma or fiber laser cutter to work with stainless steel.
Another good news we need share with we have one type of water spraying torch with fine clean cuts.which is very proper to cut stainless steel.
different cutting speed between flame cutting and plasma cuttings
Plasma Cutting speed is much faster than flame cutting.
here we shows flame parameter and its flame cutting speed
Nozzles(#) | nozzles holes | cutting thickness | Kerf radius(mm) | Preheat time(S) | Cutting speed(mm/min) | Gas pressure | |
mm | mm | mm | mm | mm/min | Oxygen | propane | |
0 | 1.0mm | 5-15mm | 1.2mm | 10-13 | 480-380 | 0.2—0.4 | >0.03 |
1 | 1.2mm | 15-30mm | 1.4mm | 12-15 | 400-320 | 0.26–0.45 | >0.03 |
2 | 1.4mm | 30-50mm | 1.6mm | 14-17 | 350-380 | 0.25–0.45 | >0.03 |
3 | 1.6mm | 50-70mm | 1.9mm | 16-19 | 300-240 | 0.3—0.5 | >0.04 |
4 | 1.8mm | 70-90mm | 2.2mm | 18-25 | 260-200 | 0.3—0.5 | >0.04 |
5 | 2.0mm | 90-120mm | 2.4mm | 24-32 | 210-170 | 0.4—0.6 | >0.04 |
6 | 2.4mm | 120-160mm | 2.9mm | 31-42 | 180-140 | 0.5—0.8 | >0.05 |
Nozzles(#) | nozzles holes | cutting thickness | Kerf radius(mm) | Preheat time(S) | Cutting speed(mm/min) | Gas pressure | |
mm | mm | mm | mm | mm/min | Oxygen | acetylene | |
0 | 0.8mm | 5-15mm | 1.0mm | 10-13 | 600-450 | 0.2—0.4 | >0.03 |
1 | 1.0mm | 10-20mm | 1.2mm | 12-15 | 480-380 | 0.26–0.45 | >0.03 |
2 | 1.2mm | 20-30mm | 1.4mm | 14-17 | 400-320 | 0.25–0.45 | >0.03 |
3 | 1.4mm | 30-50mm | 1.7mm | 16-19 | 380-350 | 0.3—0.5 | 0.03 |
4 | 1.6mm | 50-70mm | 2.0mm | 18-25 | 300-240 | 0.3—0.5 | >0.04 |
5 | 1.8mm | 70-90mm | 2.2mm | 24-32 | 260-200 | 0.3—0.5 | >0.04 |
6 | 2.0mm | 90-120mm | 2.4mm | 31-42 | 210-170 | 0.4—0.6 | >0.04 |
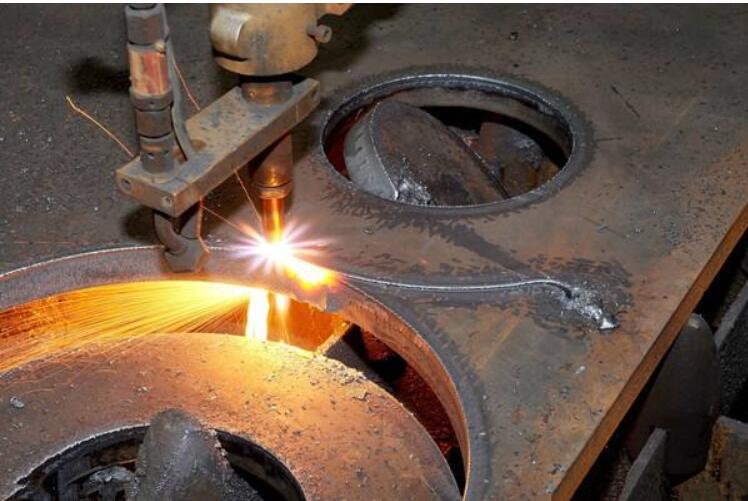
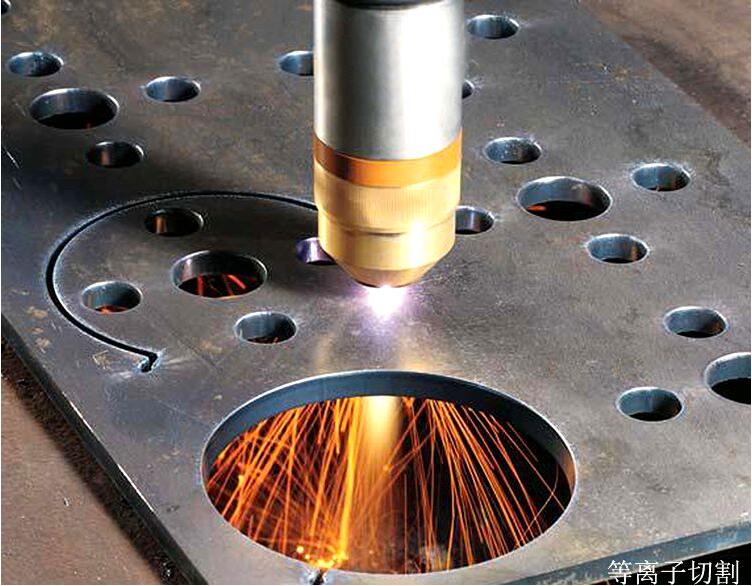